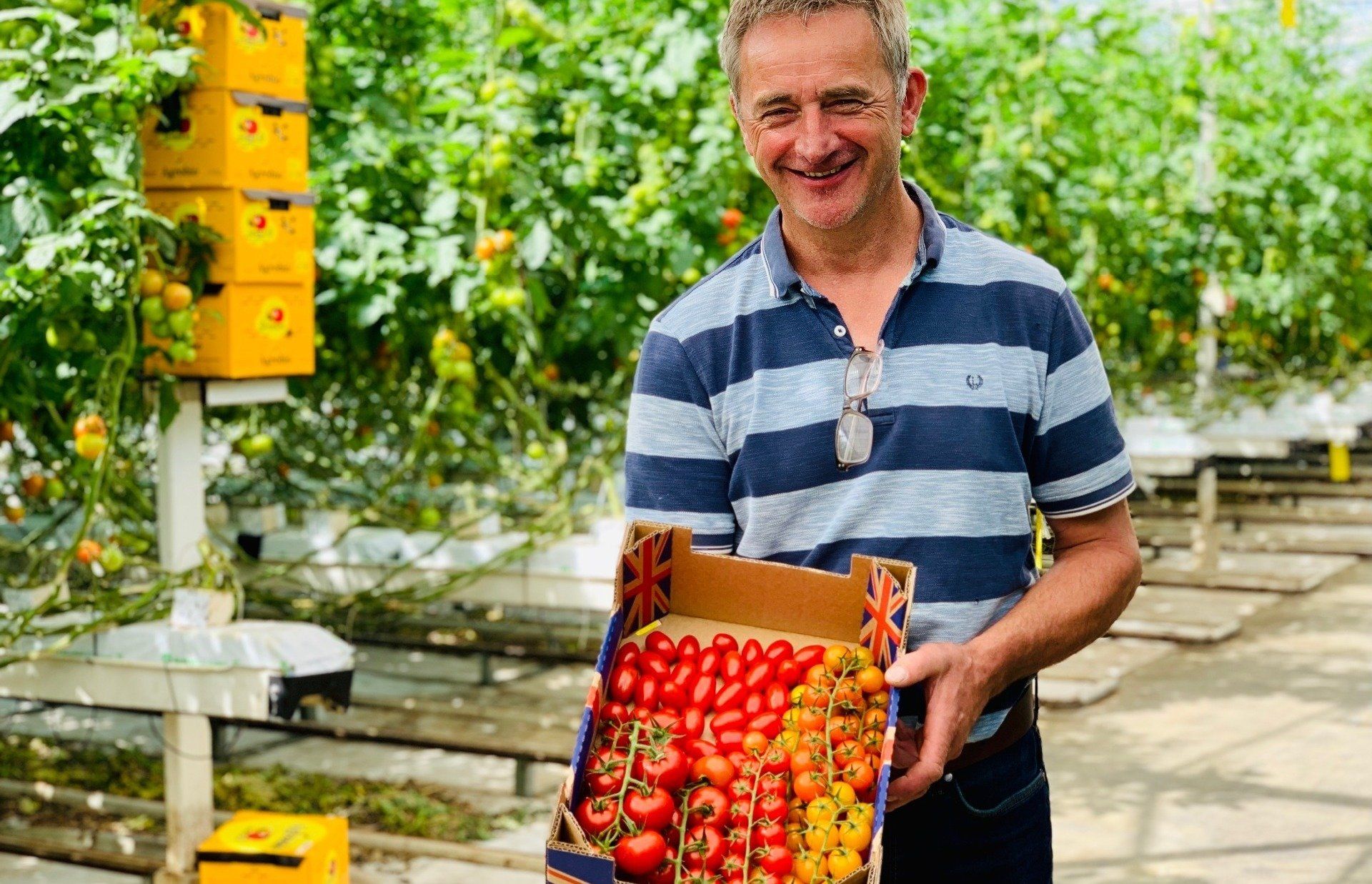
Mill Nurseries is one of our longest-standing clients and one we’ve been proud to accompany on its successful journey towards becoming one of the UK’s biggest growers.
Our relationship began two decades ago and we are about to help them deliver their latest multi-million-pound project, to expand their greenhouse growing capacity by 25 per cent.
The successful family business, established in 1962, is already East Yorkshire’s largest tomato grower and sixth largest in the UK, supplying over one hundred million tomatoes a year to supermarkets Cooperative, Waitrose, Morrisons and Lidl.
The latest build project, which will add eight more acres of glasshouses to the current 24-acre capacity at its Mill Nurseries site, has been fuelled by increased Cooperative orders and is commencing later this month, with completion planned for this November.
Pearson Electrical will be carrying out the electrical installation work required to get them up and running.
We will be creating a detailed project plan including mapping the electrical distribution to the new greenhouses, designing and building the distribution and control panels that will power the many pieces of automated equipment including fans, heating, lighting and thermal curtains – and, of course, installing the eight acres of electrical wiring.
Latest in a long line of innovations
And this is not our first collaboration with this forward-thinking business, based in Keyingham.
Three years ago, we helped to install three new combined heat and power (CHP) units, to help Mill Nurseries in their quest to heat their glasshouses as sustainably as possible. These replaced 10 old and tired 1.5 megawatt units with the latest, most energy-efficient technology in the form of three 2.5 megawatt generators.
“The glasshouse industry uses a lot of energy,” explained Hermanus de Lang, who owns and runs the business with his two brothers and sister, “especially for growing plants like tomatoes which have their origins in tropical climates like South America and need lots of heat. We need to keep our greenhouses at a steady 19 or 20-degree temperature, which is why we decided to install CHP units.”
These are basically large gas-fired engines which generate enough electricity and hot water to heat the glasshouses, exporting what isn’t used to the National Grid.
Not only that, but the flue gases they generate, which would otherwise go off into the atmosphere, adding to CO2 emissions, are diverted back into the greenhouses to again help their plants thrive.
For this project, Pearson Electrical worked alongside the manufacturers to install the state-of-the-art equipment for the three new generators. We also disconnected and removed the old units and re-routed and connected the necessary 11 kilovolt cabling. In addition, we had to modify the monitoring and control system that supports the equipment and notifies the Mill Nurseries team of the status of the CHP generators.
The CHP unit provides around 50 per cent of Mill Nurseries’ heating needs, and they take their other 50 per cent from a straw-fired biomass boiler which they installed around six years ago. This uses waste wheat straw from local farmers to create a completely renewable form of energy for their greenhouses. We were also entrusted with the full installation of this relatively new technology, including control systems and cabling.
Looking after the environment
Growing is a competitive game in a world where food production is having to keep pace with an ever-increasing population, and Mill Nurseries, which now employs over 100 people, have had to strive to stay one step ahead throughout their half a century-plus in operation.
Mill Nurseries’ water, too, comes from sustainable sources. “We collect all of our rainwater run-offs from the roofs of our greenhouses, and this all goes into a 12 million-gallon reservoir we built on site, which makes us around three-quarters self-sufficient for our water,” said Hermanus.
They were the first UK tomato growers, in the early 2000s, to install fully automatic thermal screen covers in their greenhouses, designed to reduce their heat input requirements by 25 per cent during the winter months with the added benefit of creating a better summer glasshouse environment through the shading effect of the screens.
The sheets of glass in the roofs of the new greenhouses will be significantly bigger, further minimising light obstruction and shadow from the aluminium bars used to contain them, for optimum growing efficiency.
And their sustainable growing methods also include adopting endangered bumblebees to propagate the thousands of tomato plants which stretch as far as the eye can see within their vast greenhouses.
Pest control is also done organically. “Tomatoes, like other crops, can be prey to a variety of pests, like whiteflies and leaf miners. An entomologist visits us every week during the eight-month long harvesting season to advise and provide insects like spiders to help target the pests where needs be,” added Hermanus.
A rich heritage
Hermanus’ father Gerrit set up Mill Nurseries on a smaller plot across the road from where it is now, after migrating to the UK from Holland in the 1950s. He started off growing lettuces, chrysanthemums and tomatoes in the soil.
“Ironically, given that’s where our dad hailed from, we keep a close eye on what’s coming out of Holland, which is seen very much as the centre of horticulture around the world,” added Hermanus.
“That’s where a lot of the latest innovations in growing stem from, including environmental control sensors to maximise the potential of every plant.
“Dad was a first-generation grower but spotted an opportunity to do in the UK what had been done in Holland for many years. He arrived in the UK with nothing in his pockets, no possessions or even a suitcase and not even able to speak the language.
“He started to build the business through sheer grit and determination, and just not being prepared to take ‘no’ for an answer. We’re extremely proud of what he achieved.”
Throughout the past 20 years, as well as working on Mill Nurseries’ new installations, we have looked after the certification and periodic testing of all their electrical equipment, as well as being on hand to deal with any unanticipated problems.
“While we have the ability to manually control our systems, they spend most of their lives on auto,” explained Hermanus.
“Everything has to be fully optimised, well planned and fail-safe because the slightest glitch can result in thousands of plants being potentially ruined.
“Owner Mark Pearson and his team have shared our journey so far with us. I’ve always found him and his Pearson Electrical company to be very supportive of our needs and very responsive whenever we have a breakdown, providing a level of capability and service we can trust.
“They offer a depth of knowledge and expertise which is head and shoulders above other electrical companies, giving us utter confidence every step of the way.”
Mark Pearson, owner of Pearson Electrical, said: “The care and attention that has gone into this project from everyone involved is outstanding. The site looks phenomenal – these greenhouses stand at 7.5m high, making them the tallest in the country.
“It’s been a pleasure to work with Mill Nurseries and accompany them on their successful journey towards becoming one of the UK’s biggest growers.”
If you would like our help with an industrial electrical project or problem, don’t hesitate to contact us via info@pearson-electrical.com or (01482) 225080.
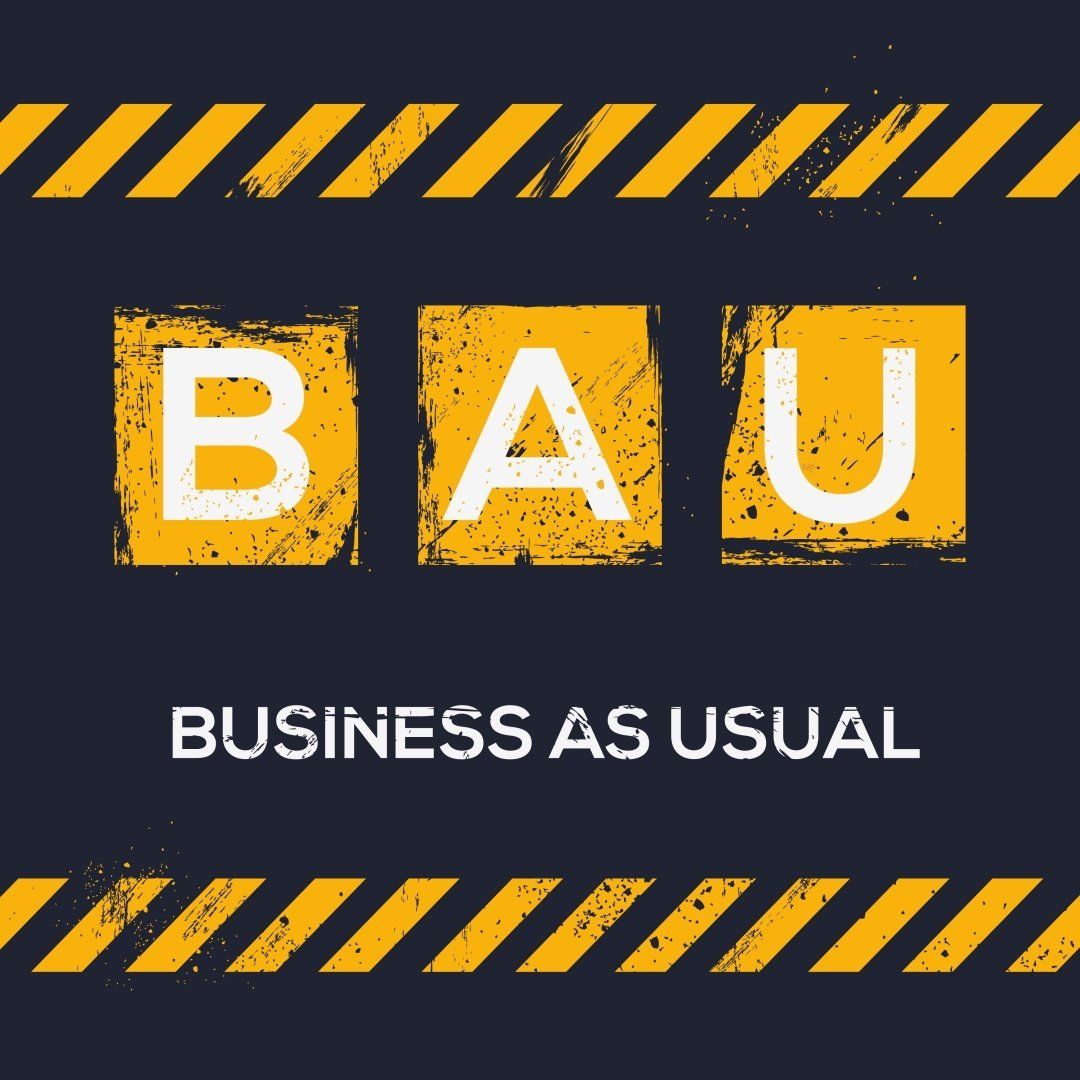